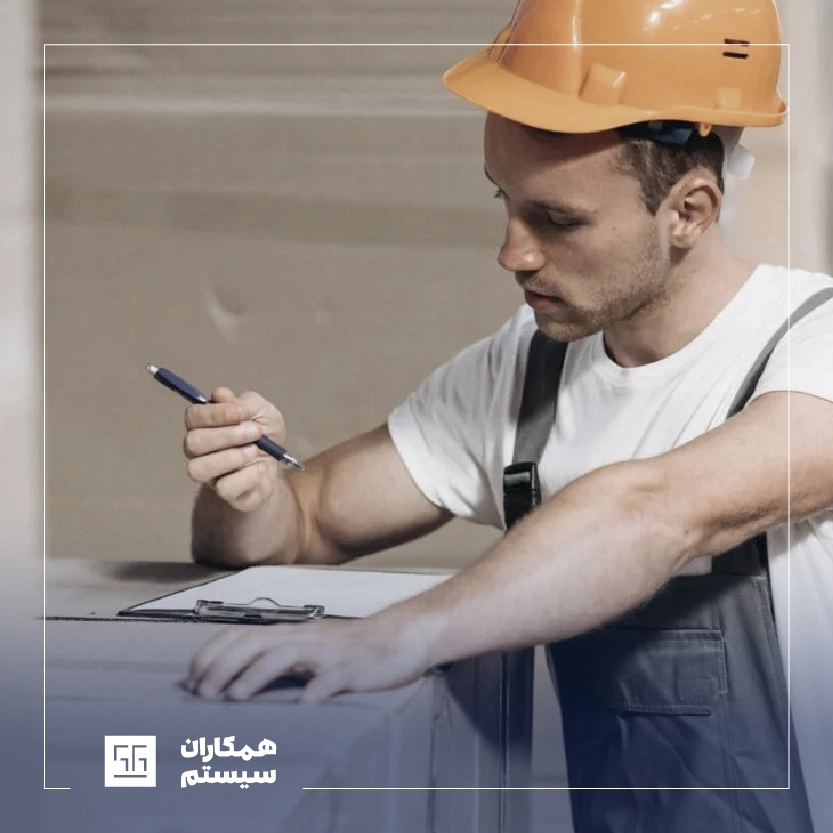
انبارداری یکی از موارد مهم در بحث لجستیک است که مسائلی نظیر سازماندهی انبار، تشکیل سیستم دریافت، حسابداری و قرار دادن موجودیها در انبار را حل میکند. امروزه انبارداری نقش مهم و بهسزایی در فرایندهای یک کسبوکار ایفا میکند.
نبود یک سیستم انبارداری دقیق مشکلات جدی برای یک کسبوکار ایجاد میکند. گمشدن کالاهای موجود، تاخیر در ارسال سفارشات، یا تاخیر در رساندن کالا به دست مشتری، تنها تعدادی از مشکلاتی است که عدم وجود یک سیستم انبارداری مناسب ایجاد خواهد کرد. این شرایط نهتنها منجر به افزایش هزینهها و کاهش رضایت مشتری میشود، بلکه اعتبار برند را نیز به خطر میاندازد.
زنجیره تأمین بدون انبار داری کارآمد مانند یک پازل ناقص است که هر تکه از این پازل عملکرد کل سیستم را تحت تأثیر قرار میدهد. در کسبوکارهای تولیدی، عدم دسترسی بهموقع به مواد اولیه، فرآیند تولید را مختل کرده و تحویل به مشتری را با تأخیر مواجه میکند. با این حال، وجود یک سیستم انبارداری منظم و دقیق، این چالشها را به فرصتی بینظیر تبدیل میکند، بهنوعی که یک کسبوکار با سیستم انبار داری مناسب، میتواند مزیت رقابتی پایداری نسبت به رقبای خود داشته باشد.
در این مقاله قصد داریم تا ضمن تعریف اینکه انبارداری چیست، در مورد تاریخچه، روشهای انبارداری، اصول انبارداری، مراحل مختلف انبارداری، فلوچارت انبارداری و دستورالعمل مرتبط با آن صحبت کنیم. پس تا پایان همراه ما باشید.
انبارداری چیست؟
همانطور که پیشتر نیز اشاره شد، انبارداری به عنوان یکی از اجزای مهم فرایند لجستیک تعریف شده و شامل اقدامات مختلفی در زمینه مدیریت تامین یا سازماندهی ورودیها و خروجیها، یا به عبارتی دیگر جریان ورود و خروج کالاها و محصولات در یک سازمان میشود.
به بیانی سادهتر، انبارداری عبارت است از فرایند ذخیرهسازی کالاهای فیزیکی یا موجودیهای یک کسب و کار در یک انبار یا تاسیسات ذخیرهسازی، پیش از آن که به فروش رسیده یا توزیع شوند. انبارها نه تنها محصولات را بهشکل ایمن ذخیرهسازی کرده و از آنها حفاظت میکنند، بلکه امکان ردیابی موقعیت و مکان یک کالا، زمان رسیدن آن، مدت زمان حضور در انبار و میزان موجودی آن را نیز فراهم میکنند.
انبارداری پایه و اساس ذخیرهسازی محصولات به حساب میآید و این امکان را فراهم میکند تا کسبوکارها بتوانند خدمات بهتری به مشتریان ارائه داده و هزینههای خود را کاهش دهند. علاوهبراین، انبار داری و ذخیرهسازی موجودی بر انواع مختلفی از فرایندهای تولید و فروش تاثیرگذار است؛ از خرید و تهیه مواد خام گرفته تا مدیریت صحیح موجودی و ارسال سفارشات به مشتریان.
تاریخچه انبارداری
مفهوم فعلی انبارداری برگرفته از مفهومی است که از زمان انسانهای نخستین آغاز شده است. انبارداری در تمدنهای اولیه، زمانی بهوجود آمد که انسانها انبارهایی برای ذخیره مواد غذایی اضافی جهت مقابله با زمستانهای طولانی و قحطی ایجاد کردند. حدود 2200 سال پیش، رومیان انبارهای بزرگی برای ذخیره غلات و پوشاک در نزدیکی رود تیبر ساختند تا کالاها مستقیماً از کشتیها تخلیه و انبار شوند. در بریتانیا، نخستین استفاده از واژه “انبار” به دهه 1300 میلادی برمیگردد که برای نگهداری کالاهایی مانند ظروف شیشهای و سرامیک استفاده میشد.
در طول انقلاب صنعتی در اواخر دهه 1700، انبارداری به بخشی جداییناپذیر از کسبوکارها تبدیل شد. تولید انبوه و اختراع ماشینآلات صنعتی باعث افزایش نیاز به انبارهای بزرگ برای ذخیره و توزیع محصولات شد. با پیشرفت فناوری، لیفتراکها، پالتها، و قفسههای بلند در طول جنگ جهانی دوم معرفی شدند.
در دهههای 1960 و 1970، سیستمهای خودکار انبارداری (AS/RS) توسعه یافتند، اما از اواخر دهه 1980 تمرکز به سمت کاهش موجودیها و تحویل بهموقع تغییر کرد. انبارداری امروز به انبارهای پیشرفته و چند میلیون دلاری تبدیل شده است، اما همچنان در حال تکامل است تا با نیازهای مدرن تطبیق یابد.
بررسی تفاوت انبارداری با ذخیرهسازی و پخش
گاهی از اوقات 2 واژه انبارداری و ذخیرهسازی بهجای یکدیگر استفاده میشوند، اما آیا این دو مفهوم یکسان هستد یا با یکدیگر تفاوت دارند؟ دو مفهوم انبارداری و ذخیرهسازی در عمل با یکدیگر تفاوت جزئیای دارند که توجه به آن بسیار مهم است. درست است که انبار نیز محلی است که از آن برای حفظ و نگهداری انواع کالاها استفاده میشود، اما این حفظ و نگهداری دائمی نبوده و کالاهای موجود در انبار همیشه در جریان هستند. برای مثال کارخانه تولید مواد غذایی را تصور کنید که مواد اولیه را خریداری کرده و آن را در انبار نگهداری میکند، اما این حفظ مواد اولیه در انبار همیشگی نیست و ممکن است پس از گذشت یک روز، مواد اولیه از انبار به خط تولید منتقل شوند.
در مقابل، مفهوم ذخیرهسازی معمولا به نگهداری و ذخیره آن دسته از داراییهای غیرتجاری اشاره دارد که برای احتیاط و استفادههای آتی، نگهداری و کنار گذاشته میشوند. برای مثال همین کارخانه تولیدی ممکن است یک خط تولید یدکی یا تجهیزات جایگزین را برای استفاده در شرایط اضطراری یا تعمیرات نگهداری کند. این تجهیزات نمونهای از ذخیرهسازی هستند، زیرا به صورت مستقیم در فرآیند جاری استفاده نمیشوند.
در حالی که انبار داری و ذخیرهسازی بر نگهداری و مدیریت کالاها متمرکز هستند، پخش بر انتقال کالاها و تضمین دسترسی سریع و بهینه برای مشتریان تمرکز دارد. این سه مفهوم مکمل یکدیگرند و بدون وجود هر یک از 3 مفهوم در یک تولیدی، جریان تولید بهخوبی عمل نمیکند.
اهمیت انبارداری در لجستیک
انبارداری مقولهای مهم و ضروری در مدیریت زنجیره تامین محسوب میشود؛ چرا که طی فرایندهای زنجیره تامین، کالاها و محصولات از سمت تولیدکننده به دست مصرفکننده نهایی آنها رسیده و چنانچه عملکرد یک انبار بیفایده و نامطبوب باشد، ممکن است کل زنجیره تامین را تحت تاثیر خود قرار دهد. به عنوان مثال، کمبود کالا یا تاخیر در ارسال آنها از سمت انبار، میتواند اثرات زیانباری بر زنجیره تامین و در نتیجه عملکرد سازمان داشته باشد.
هدف از به کار بردن قوانین انبارداری، پشتیبانی از فرآیندهای تولید است که این امر با حفظ منابع، مواد و بستهبندی کافی برای تولید، زمینه را برای داشتن خروجیها و محصولات بدون مشکل و وقفه زمانی فراهم میکند.
در واقع انبارها امکان دسترسی دائمی به محصولات و کالاها و امکان دریافت سیستماتیک کالاهای نهایی و تحویل به گیرنده مورد نظر را ایجاد میکنند. لازم به ذکر است که انبارها با فراهم آوردن دسترسی مداوم به منابع مورد نیاز برای تکمیل یک اقدام تبلیغاتی یا تولید مجموعههای تبلیغاتی، از فرآیندهای بازاریابی نیز پشتیبانی میکنند.
انواع انبارها کدامند؟
انبارها انواع مختلفی دارند که در ادامه آنها را معرفی کرده و به توضیح مختصری در مورد هریک از آنها میپردازیم.
انبارهای مواد خام و اجزا
این دسته از انبارها از مواد خام نگهداری کرده و همیشه در موقعیتی قرار دارند که مواد خام را از انبار به فرآیند تولید یا مونتاژ هدایت میکنند.
انبارهای در جریان فرایند کار
این انبارها از محصولات و ماژولهای نیمه تکمیل شده در نقاط مختلف خط تولید یا خطوط مونتاژ نگهداری میکنند.
انبارهای کالاهای نهایی
این دسته از انبارها معمولاً از موجودی برای متعادلسازی تغییرات میان برنامههای تولید و تقاضا نگهداری میکنند. معمولاً این انبارها در نزدیکی کارخانه تولید قرار دارند.
انبار توزیع و مراکز توزیع
انبارهای توزیع ، محصولات را از نقاط تولیدی مختلف و برای ارسال ترکیبی به مشتریان جمعآوری میکنند. به طور معمول این انبارها در مرکز محل تولید یا پایگاه مشتریان قرار دارند.
انبارها و مراکز انجام سفارش
این انبارها سفارشهای کوچک را برای مصرفکنندگان فردی دریافت، بستهبندی و ارسال میکنند.
انبارهای محلی
این انبارها عمدتاً به منظور پاسخگویی به تقاضای مشتریان ایجاد میشوند. در اغلب موارد کالاها بهشکل تکی از این انبارها انتخاب شده و روزانه برای مشتری ارسال میشوند.
انبارهای خدمات ارزش افزوده
در این انبارها فعالیتهای اصلی سفارشیسازی محصول مانند بستهبندی، برچسبگذاری، علامتگذاری، قیمتگذاری و پردازش محصولات برگشتی انجام میشود.
انواع مختلفی از انبار وجود دارند که بسته به نوع عملیاتی که در آنها انجام میشوند، نامگذاری و بهکار گرفته میشوند.
همچنین طبقهبندی دیگری نیز از انبارها بر اساس منطقه جغرافیایی انبارها وجود دارد که عبارتند از:
انبار متمرکز
تمرکز معمولا به تخصیص خدمات انبارداری به یک واحد تجاری خاص اشاره دارد که به کل شرکت خدمات ارائه میدهد. در این انبارها تصمیمات در یک انبار مرکزی و برای کل شبکه اخذ میشوند. ویژگیهای اصلی یک انبار متمرکز مواردی مانند کنترل، کارایی و اقتصادی بودن آنها است.
انبار غیر متمرکز
رویکرد غیرمتمرکز به هریک از انبارهای تجاری ، استقلال و تسلط نسبت به منابع خود و بدون توجه به سایر انبارها را اعطا میکند؛ مگر اینکه برحسب ضرورت، سیاستهای کلی و سازمانی خاصی برای انبارداری وجود داشته باشد. در این رویکرد، هر انبار موثرترین استراتژی خود را بدون در نظر گرفتن تأثیرات آن بر سایر انبارهای موجود در شبکه تدوین میکند. از ویژگیهای اصلی رویکرد غیرمتمرکز میتوان به توانمندسازی هر یک از واحدهای کسبوکار بهشکل تکی، انعطافپذیری و خدمتدهی بهتر اشاره کرد.
علاوهبر این در دستهبندی دیگری، انبارها از لحاظ نوع ساخت و ساختمان به 3 دسته تقسیم میشوند:
انبار بسته
انبارهای بسته، فضاهایی کاملاً ایزولهای هستند که از سقف، دیوارها و دربهای مقاوم تشکیل شدهاند. این انبارها به طور کامل از کالاها در برابر عوامل محیطی مانند بارش باران، تابش مستقیم آفتاب، گرد و غبار و تغییرات دمایی محافظت میکنند.
انبار مسقف
انبارهای مسقف، مانند انبارهای بسته دارای سقف هستند اما اطراف آنها پوشیده نیست و محیطی آزاد دارند. این انبارها معمولا نیمهباز هستند و در برابر شرایطی مانند بارش باران از کالاها محافظت میکنند، اما در برابر باد و طوفان یا گردوغبار عملکرد مناسبی ندارند.
انبار باز
انبارهای باز شامل فضاهای وسیعی هستند که کاملاً در هوای آزاد قرار دارند و بدون سقف یا دیوار ساخته میشوند. این انبارها بهطور مستقیم در معرض شرایط محیطی هستند و معمولاً برای کالاهایی استفاده میشوند که مقاومت بالایی در برابر تغییرات آبوهوایی دارند.
تعاریف کاربردی و اصطلاحات انبارداری
در ادامه به معرفی برخی از رایجترین اصطلاحات انبارداری میپردازیم. شناخت و یادگیری معنای این عبارتها درک و برقراری ارتباط با دیگران در زمینه انبارداری و زنجیره تامین را آسانتر میکند.
- واحد (Unit): یک کالا یا محصول فیزیکی خاص در انبار.
- سفارش (Order): تمام محصولاتی که در قالب یک تراکنش از سمت مشتری انتخاب و خریداری شدهاند.
- 3PL (شرکتهای لجستیکی طرف سوم): شرکتهای لجستیکی طرف سوم یا به اختصار 3PLها به آن دسته از شرکتهایی گفته میشود که سازمانهای تولیدی یا خدماتی ، مدیریت یک یا چندین انبار خود را به آنها برونسپاری و یا واگذار میکنند.
- بارکد: نوعی علامتگذاری روی محصولات که متشکل از تعدادی نوار و خط بوده و برای شناسایی نوع محصولات موجود در انبار بهکار گرفته میشود. برای خواندن اطلاعات این علامتهای رمزگذاری شده از دستگاه اسکن استفاده میشود.
- انتخاب دستهای (Batch picking): یکی از فرآیندهای آمادهسازی سفارش که در آن تمام موارد، در چندین سفارش، توسط فردی که سفارشها را آماده میکند و کالاها را از انبار برمیدارد، انتخاب میشود.
- سیستم مدیریت انبار(WMS): یک نرم افزار انبار که تمامی عملیات انبار از جمله دریافت، تحویل، برداشت، حملونقل و موجودی را پیگیری میکند.
- کد QR: کد پاسخ سریع (QR) یک کد قابل اسکن است که از چندین مربع سیاه و سفید مختلف تشکیل شده است. دوربینها یا گوشیهای هوشمند این امکان را دارند که آن را اسکن کرده و کاربر را به یک URL ذخیرهشده یا سایر اطلاعات هدایت کند.
- دریافت (Receiving): فرآیندی که شامل دریافت فیزیکی کالا، بازرسی آنها به منظور تایید صحت و شناسایی هرگونه آسیب احتمالی در آنها، تعیین محل نگهداری انبار و تحویل به آن مکان میشود.
- منطقه برداشت (Zone Picking): یکی از فرایندهای آمادهسازی سفارش است که طی آن، اقلام یک سفارش را از مناطق اختصاصیافته به آنها در انبار انتخاب میکنند تا بعداً برای حمل و نقل مونتاژ شوند.
- سفارش خرید: سفارش خرید برگهای است که از جانب خریدار برای تامینکننده ارسال میشود و از طریق آن، کالاهای مدنظر را سفارش میدهد. در برگه سفارش خرید معمولاً نوع کالا، مقدار و قیمت توافقی آن ذکر میشود.
- قفسهبندی کردن: انتقال سفارشهای دریافتی از محل دریافت آنها به محل ذخیره نهایی در انبار، ثبت مسیر حرکتی آنها و محلی که این سفارشها در آنجا ذخیره میشوند.
- بارنامه: برگهای است که جزئیات اقلام موجود در یک محموله را نشان داده و به عنوان رسیدی است که حملکننده کالا، به گیرنده آن در انبار تحویل میدهد.
- تفکیک سفارش: فرآیندی از آمادهسازی سفارش ، که در آن مامور آمادهکننده سفارش همه آیتمهای هر سفارش را انتخاب میکند.
- انبار عبوری: انتقال مستقیم محصولات از منطقه تحویل به سمت منطقه بارگیری و توزیع، به جای نگهداری و ذخیرهسازی طولانی مدت آنها.
- خط (Line): محصولات متعلق به یک سفارش که دارای کد جهانی کالا (UPC) یا شناسه کالا(SKU) مشابه هستند.
- پرکردن (Replenishment): فرایند انتقال موجودی از یک محل ذخیرهسازی ثانویه به یک محل ذخیرهسازی ثابت. این اصطلاح همچنین میتواند به فرآیند جابهجایی موجودی میان مراکز توزیع یا از جانب تامینکنندگان برای پاسخگویی به تقاضای مشتری اشاره داشته باشد.
آشنایی با اصطلاحات انبارداری به شما کمک میکند تا درک بهتری نسبت به مباحث مربوط به این حوزه داشته باشید.
منظور از عملیات انبار چیست؟
عملیات انبارداری به فرآیندهایی گفته میشود که در یک انبار پیرامون جابجایی کالا و رهگیری موجودی اتفاق میافتند. عملیات انبارداری شامل اقداماتی مانند دریافت موجودی، قرادادن هریک از موجودیها در جای مخصوص و مشخص خود (نظیر قفسهها) و ارسال محصول یا کالا به مقصد بعدی هستند.
عملیات انبار کارآمد به حفظ موارد زیر کمک میکند:
- کاهش هزینههای انبارداری
- دریافت و ارسال به موقع موجودیها از انبار
- افزایش بهرهوری نیروی کار
- در دسترس و در اختیار داشتن موجودیهای کافی از هریک از محصولات انبار
- در اختیار داشتن ظرفیت اضافه در انبار
- فضای ذخیرهسازی بهینه شده در انبار
- استفاده اثربخش از تجهیزات انبار
- مشتریان راضی
مدیریت انبار شامل چه اقداماتی است؟
مدیریت انبار عبارتست از: اجرای استراتژیک عملیات در یک انبار، بهشکل روزانه و با هدف ارتقا، بهبود و تضمین عملیات اجرایی. مدیریت انبارداری به معنای نظارت بر تمامی کارکنان انبار، آموزش، موجودی، تجهیزات، ایمنی و امنیت، روابط با شرکتهای حمل و نقل، کمبودهای انبار و غیره است. موارد زیر از جمله مسئولیتهای مدیر انبار هستند:
- پیشبینی و مدیریت حجم و نیروی کار درنظر گرفته شده برای انبار
- کسب اطمینان در مورد استفاده از تجهیزات ایمنی مناسب و رعایت بهترین شیوههای ایمنی در تمام زمانها
- انطباق با قوانین و الزامات نهادهای نظارتی
- برنامهریزی و مدیریت مداوم عملیات با رشد و پیچیده شدن کسبوکار
- ایمن و در دسترس نگه داشتن کالاها و انجام ممیزی انبار در صورت نیاز
- ارائه دستورالعملهای روشن و واضح در مورد نحوه دریافت، بازگشایی، بازیابی، بستهبندی و ارسال موجودیهای انبار
- ثبت تمامی محمولههای ورودی و خروجی انبار و جمعآوری اسناد و مدارک مناسب
سیستم مدیریت انبار (WMS) چیست؟
سیستم مدیریت انبار (WMS) نوعی نرم افزار است که ابزارهای لازم را برای مدیریت عملیات انبار و جابهجایی موجودی، با هدف صرفهجویی در زمان و حذف فرآیندهای دستی، فراهم میکند. سیستمهای مدیریت انبار به بهینهسازی موجودی ، رهگیری، عملیات انبارداری ، توزیع حجم کار و حملونقل کمک موثری میکنند. این دسته از سیستمهای انبارداری ، به هریک از کسبوکارها دید و بینش بیسابقهای نسبت به هر اقدامی که در انبار اتفاق میافتد، میدهد.
جریان فرآیند سیستم مدیریت انبار
هر انبار باید مکان و چگونگی انتقال محصولات را مشخص کند که این جریان فرآیند مدیریت انبار نامیده میشود. آنچه در این فرایند اهمیت دارد، این است که پیش از شروع فرایند سفارشگیری، جریان مناسب برای مدیریت انبار را مشخص کنید.
دلایل متعددی برای اهمیت جریان فرآیند انبار وجود دارد. یک جریان فرآیند مدیریت انبار که به خوبی طراحی شده باشد، نه تنها باعث صرفهجویی در زمان و هزینه کسبوکار شما میشود؛ بلکه تمام مراحل عملیات انبار شما را مشخص میکند و به این ترتیب قدرت تمرکز روی انجام کارها در انبار را افزایش میدهد.
جریان فرآیند سیستم مدیریت انبار یک نمودار خطی ساده یا بصری است که فعالیتهای اصلی انبار شما را نشان میدهد. در واقع جریان فرآیند سیستم مدیریت انبار جزئی فرعی از انبار است که نحوه دریافت کالا، فرآیندی که هر کالا در انبار طی میکند، نحوه ارسال و هر مرحلهای که در بین آنها قرار داشته باشد را نشان میدهد.
آشنایی با فلوچارت انبارداری
فلوچارت انبارداری ، حرکت کالاهای انبار را در یک قالب بصری نشان میدهد. انواع فلوچارت انبار را میتوان حداقل در قالب سه مرحله تقسیم کرد: دریافت، ذخیرهسازی و حمل و نقل. این نوع از فلوچارت انبارداری برای انبارهای کوچک یا خطوط تولید محدود، جایی که محصولات پس از دریافت از یکدیگر جدا نمیشوند، بهترین کارکرد را دارد. در اینجا مثالی از نمودار جریان ساده انبار به تصویر کشیده شده است:
مثالی از نمودار جریان ساده انبار
فلوچارت انبارداری متوسط و یا اصطلاحا مدیوم، رایجتر بوده و دارای مراحل بیشتری هستند. این نوع از فلوچارت ها برای شرکتهای متوسط تا بزرگ یا آنهایی که محصولات زیادی دارند، مفید است. فلوچارت های متوسط علاوه بر دارا بودن سه مرحله فلوچارت های ساده، شامل بخشهایی برای انجام امور مقدماتی هم هستند؛ بخشهایی نظیر قسمتهای متعددی برای ذخیرهسازی، اتاق ذخیرهسازی سرد و گرم، ناحیه بستهبندی و جمعآوری و بخش تجمیع و حملونقل. یک فلوچارت انبارداری مدیوم میتواند در قالب نمودار زیر باشد:
مثالی از نمودار جریان متوسط انبار
فلوچارت انبارداری در حالت پیچیده بسته به نیاز محصول ممکن است 10 مرحله یا بیشتر داشته باشند. استفاده از این فلوچارتها بیشتر در مواردی رایج است که مثلا دمای محصولات باید کنترل شوند، موجودیهای انبار ارزش بسیار بالایی داشته یا محصولات از اجزای زیادی تشکیل شده باشند.
مراحل در فلوچارت انبار پیچیده ، متنوع بوده و میتوانند شامل انبار ذخیره، منطقه حملونقل، تولید، کنترل کیفیت و آمادهسازی محصولات برای حملونقل باشد. براساس نوع کسبوکار، هریک از این مراحل میتوانند دستخوش تغییر شوند. نمونهای از فلوچارت انبارداری پیچیده در زیر آورده شده است:
مثالی از نمودار جریان پیچیده انبار
اصول و روش انبارداری
یکی از موضوعات مهم در مدیریت انبارداری ، طراحی انبار و اصول مربوط به آن است. انبارها چه کوچک باشند و بهشکل دستی و غیراتوماتیک فعالیت داشته باشند و چه بزرگ و کاملا اتوماتیک، در طراحی و راهاندازی آنها باید سه اصل زیر مورد توجه قرار گیرد:
- معیارهای طراحی
- فناوری حملونقل
- طرح و برنامه ذخیرهسازی
1.معیارهای طراحی انبار
معیارهای طراحی انبار به ویژگیهای مرتبط با امکانات فیزیکی، گردش و حرکت محصول در انبار میپردازد. سه فاکتوری که در فرآیند طراحی انبار باید در نظر گرفته شوند، عبارتند از: تعداد طبقات انبار، ارتفاع فضای انبار و جریان محصولات انبار.
- تعداد طبقات در انبار: طراحی یک انبار ایده آل عموما به یک طبقه محدود میشود تا الزامی برای بالا و پایین بردن محصولات وجود نداشته باشد. استفاده از آسانسور برای جابهجایی محصول از یک طبقه به طبقه دیگر انبار، نیازمند زمان و انرژی است. همچنین خود آسانسور نیز میتواند به یک گلوگاه در انبار تبدیل شود، چرا که تعداد آنها در انبارها محدود است، اما متقضیان استفاده از آنها زیاد! اگرچه با توجه به هزینهبر بودن متراژ بالای زمین، تاکید بر انبارهای تک طبقهای همیشه امکانپذیر نیست؛ اما بهتر است که انبارها محدود به یک طبقه باشند.
- ارتفاع فضای انبار: صرفنظر از متراژ انبارها، طراحی آنها باید به گونهای باشد که ارتفاع هر طبقه از انبار، در حداکثر میزان خود باشد. اکثر انبارها دارای سقفهای 20 تا 30 فوتی هستند (1 فوت = 12 اینچ؛ 1 اینچ = 2.54 سانتیمتر)، اما انبارهای مدرن خودکار و مرتفع میتوانند به طور موثر از ارتفاع سقف تا 100 فوت استفاده کنند. لازم به ذکر است که از طریق استفاده از قفسه یا سایر تجهیزات، باید بتوان محصولات را تا سقف ساختمان انبار ذخیره کرد.
- جریان محصولات: طراحی انبار همچنین باید به گونهای باشد که امکان جریان حرکت مستقیم محصول از طریق انبار را فراهم کند؛ چه کالاها ذخیره شده باشند چه نه. به طور کلی، این موضوع بدان معناست که محصول باید در یک انتهای انبار دریافت، در وسط آن ذخیره شده و سپس از انتهای دیگر آن ارسال شود. جریان مستقیم محصول تراکم و سردرگمی را به حداقل میرساند.
2.فناوری حملونقل
اصل دوم بر اثربخشی و کارایی فناوری حملونقل مواد در انبار تمرکز دارد. عناصر این اصل عبارتند از: تداوم حرکت و مقیاس حرکت.
- تداوم حرکت: تداوم حرکت به این معنی است که بهتر است تجهیزاتی که وظیفه جابهجایی مواد یا قطعهها در انبار را به عهده دارند، حرکات و جابجاییهای طولانیتری انجام دهند تا اینکه تعداد زیادی از این تجهیزات بهشکل جداگانه و بخش بخش، مواد و قطعات را در انبار جابهجا کنند. مبادله محصول میان گردانندههای مختلف یا جابجایی آن قطعه به تجهیزات دیگر، باعث هدر رفتن زمان و افزایش احتمال آسیب به آنها میشود. بنابراین، به عنوان یک قاعده کلی، جابجاییهای کمتر در انبار ترجیح داده میشود.
- مقیاس حرکت: مقیاس در حرکت نشان میدهد که تمام فعالیتها و جابهجاییهایی که در انبار صورت میگیرد، باید بیشترین مقدار ممکن از مواد یا قطعات را جابهجا کنند. به بیانی دیگر، به جای جابجایی هر یک از محصولات یا قطعات بهشکل تکی، این جابجاییها باید به صورت گروهی انجام شده و بهشکل همزمان جابهجا شوند. با وجود اینکه این موضوع میتواند پیچیدگی فعالیتهای یک فرد را در انبار افزایش دهد، اما این اصل تعداد فعالیتها و هزینه ناشی از آن را کاهش میدهد.
3.طرح و برنامه ذخیرهسازی
طراحی انبار باید ویژگیهای محصول، به ویژه آنهایی که مربوط به حجم، وزن و ذخیرهسازی آن میشود را مدنظر قرار دهد. حجم محصول یکی از نگرانیهایی است که هنگام تعریف برنامه ذخیرهسازی انبار باید به آن پاسخ داده شود. محصولاتی که حجم فروش بالایی دارند، باید در مکانی ذخیره شوند که فاصله جابهجایی آن به حداقل برسد؛ مکانهایی مانند نزدیک راهروهای اولیه یا قفسههای ذخیرهسازی که پایینتر قرار دارند. چنین مکانهایی مسافت حرکت و حمل طولانی مدت محصول را در انبار به حداقل میرساند.
برعکس، محصولات کم حجم را میتوان در مکانهایی که از راهروهای اصلی انبار دور هستند یا در قفسههای ذخیرهسازی که بالاتر قرار دارند، قرار داد. اقلام نسبتاً سنگین نیز باید در مکانهایی از انبار با سطح پایین قرار گیرند تا تلاش زیادی برای بلند کردن آنها انجام نشود.
فرقی نمیکند انبار شما چه اندازهای داشته باشد، رعایت اصول طراحی، حملونقل و ذخیرهسازی از مهمترین مواردی است که باید مورد توجه قرار بگیرند.
مشکلات رایج در انبارداری
در زمانهای گذشته که امور مربوط به انبار به شکل دستی انجام میشدند، فرایند انبارداری بسیار سادهتر از امروز تلقی میشد. در واقع بزرگترین مشکلات در آن زمان، نبود بارکد کالاها و استفاده ناکارآمد از فضای انبار بود. در دنیای اینترنتی امروزی، تغییرات زیادی رخ داده است و با توسعه فناوریها، همه چیز حتی سادهتر از روزهای قبل، با کارایی بیشتر، صرف زمان کمتر و کسب مزیت رقابتی با صرفهجویی اقتصادی بالقوه بهنظر میرسد.
کاربرد فناوریهای مختلف مانند کاربرد RFID روشهای انبارداری را با سرعتی بیشتر و با خطای بسیار کمتر متحول کرد و در آنها تغییر زیادی ایجاد کرد. اگرچه هرروزه فناوریهای زیادی در حال پیشرفت هستند، اما مشکلات زیادی نیز ایجادکردهاند که مدیریت انبارداری را پیچیدهتر میکنند. این موضوع به نوبه خود بر کل مدیریت زنجیره تامین اثر میگذارد.
برخی از مشکلات موجود در انبارهای امروزی به شرح زیر است:
- خودکارسازی تمام عملیات مکانیزه یا دستی در انبار
- برآوردهساختن نیازهای مشتریان بدون سفارشیسازی
- سازگاری با زنجیره تامین جهانی مقرون به صرفه
تغییرات روند انبارداری و اهمیت راهکارهای نرم افزاری در مدیریت انبار
با توجه به تغییر روند در مشاغل، عملیات انبارداری و توزیع نیز باید با تغییرات در حال ظهور و نیازهای فزاینده مشتریان سازگار شود. اصطلاح «جهانی سازی» ، تغییرات زیادی را در لجستیک به همراه داشته است. عملیات توزیع انبار امروزه تاکید بیشتری بر موجودیهای کمتر، اندازه سفارشهای کوچکتر، کاتالوگهای واحد نگهداری موجودی یا SKU بزرگتر، تحویل سریعتر سفارش، افزایش بستهبندی سفارشی و خدمات ارزش افزوده دارند. در گذشته کسبوکارها تنها روی مراکز توزیع محلی متمرکز بودند، اما امروزه سازمانها بهجای داشتن تنها یک شبکه توزیع، تاکید و اهمیت بیشتری بر داشتن مراکز توزیع جهانی دارند.
برای رویارویی با این روندهای در حال تغییر، امروزه اکثر شرکتها، فناوریهای جدیدی مانند سیستمهای مدیریت انبار (WMS) و سیستمهای مدیریت حمل و نقل (TMS) را بهکار گرفته و برخی نیز تصمیم به طراحی مجدد فرآیندها و امکانات برای پاسخگویی به نیازهای نوظهور و همچنین کاهش هزینهها و بهبود سطح خدمات به مشتریان گرفتهاند. برخی از مشاغل نیز یک گام جلوتر رفته و تصمیم به استقرار اتوماسیون کل عملیات انبارداری گرفتهاند. برخی نیز تمام عملیات انبارداری خود را به شرکتهای لجستیکی طرف سوم (3PL) برونسپاری کردهاند.
استفاده از راهکارهای نرم افزاری برای مدیریت بهتر انبارها ، یکی از مواردی است که در دنیای امروزی، به ایجاد یکپارچگی در دادهها و ایجاد شفافیت کمک میکند. نرم افزار خرید تدارکات و لجستیک همکاران سیستم با ارائه نرم افزارهای مختلفی از جمله نرم افزار انبار و حسابداری انبار، پذیرش و توزین، مدیریت سریال و مدیریت جانمایی در انبار به شما کمک میکند تا به مدیریت هرچه بهتر انبار خود بپردازید. با استفاده از ERP تدارکات و لجستیک همکاران سیستم میتوانید برنامهریزی و تصمیمگیری مناسبی برای کنترل هزینههای نگهداری موجودی، سفارشگذاری و تامین بهموقع کالا و پیشگیری از کمبود موجودی داشته باشید. برای کسب اطلاعات بیشتر با ما تماس بگیرید.
منابع:
- inviarobotics.com
- bluecart.com
- vskills.in
- magenest.com
- skunexus.com
- linkedin.co