ماژول کنترل تولید راهکاران
تهیه برنامههای تولید با در نظر گرفتن نیازمندیهای مواد اولیه و ظرفیتهای مراکز تولیدی از دغدغههای اصلی مدیران و کارشناسان برنامهریزی تولید است. پیشبرد تولید براساس سفارش مشتریان یا برنامههای کلان تولید، ارسال به موقع و به اندازه مواد اولیه طبق BOM به خطوط تولید با در نظر گرفتن میزان موجودی انبارها و پای کار خطوط، اندازه بسته کالاها، تاریخهای انقضا و موجودی جایگزین کالاها موجب کاهش توقفات تولید به دلیل کمبود موجودی میشود. همچنین با کنترل میزان مصارف و ساعتهای عملکرد، انحرافات برنامهها شناسایی شده و میتوان اقدامات اصلاحی برای رفع آنها اتخاذ کرد.

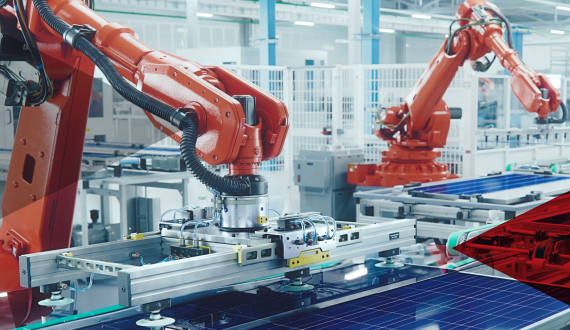
یکی از ماژولهای نرم افزار مدیریت تولید و مدیریت کارخانه راهکاران، کنترل تولید است. این ماژول با امکاناتی از قبیل مدیریت اطلاعات مهندسی کالاها، سفارشگذاری مراکز تولیدی، کنترل موجودی پای کار، شارژ به اندازه و به موقع خطوط تولید، ثبت گزارشات تولید و کنترل انحرافات براساس برنامهها، مدیریت ضایعات و دوبارهکاریها و مدلهای متفاوت ردیابی بچ در کل فرایند تولید، نیازهای صنایع مختلف را پوشش میدهد. بخشی از این امکانات مخصوص صنایع خاص طراحی شده و میتواند با توجه به شرایط خطوط تولید و دستورالعملهای اجرایی شرکتها متناسبسازی شود.
مدلهای ارائه نرم افزار کنترل تولید
راهکاران ویژه کسبوکارهای بزرگ
مدل استفاده از نرم افزار به صورت خرید لایسنس نرم افزار
نحوه دسترسی محدود به شبکه داخلی سازمان
تامین زیرساخت و امنیت اطلاعات بر عهده مشتری
بهروزرسانیها توسط تیم IT سازمان شما
نیازمند تغییرات در زیرساختهای داخلی سازمان
راهکاران ابری ویژه کسبوکارهای متوسط و کوچک
مدل استفاده از نرم افزار به صورت پرداخت حق اشتراک
نحوه دسترسی بدون محدودیت مکانی، زمانی و بر بستر ابر
تامین زیرساخت و امنیت اطلاعات بر عهده همکاران سیستم
بهروزرسانیها به صورت خودکار توسط همکاران سیستم
امکان تغییر سریع منابع با توجه به نیازهای سازمان
مزایای ماژول کنترل تولید راهکاران
اطمینان از پاسخگویی برنامههای تولید به تقاضای مشتریان
استفاده مناسب از ظرفیت خطوط تولید برای پاسخگویی به تقاضای مشتریان
برنامهریزی خطوط تولید و پیمانکاران بر مبنای برنامه کلان تولید یا سفارش مشتریان
ارسال به موقع و به اندازه مواد و کنترل موجودیهای پای کار خطوط تولید
کنترل و پایش آمار تولید، ضایعات و دوبارهکاریها
ردیابی محصولات از تامین مواد اولیه، طی فرایند تولید و پس از فروش به مشتری
ویژگیهای ماژول کنترل تولید راهکاران
-
مهندسی محصولات
یکی از مهمترین بخشهای هر سیستم برنامهریزی و کنترل تولید، تعریف اطلاعات مهندسی محصولات است. تعیین ساختار محصول (BOM) و فرایند تولید آن (Routing)، پیشنیاز هرگونه فعالیت برنامهریزی، سفارشگذاری، زمانبندی و اجرای تولید است.
-
ارسال مواد و قطعات به خطوط تولید
این ماژول کمک میکند تا مراکز تولیدی را با در نظر گرفتن BOM و به مقدار سفارشهای تولید، با اعمال سیاست مصرف متنوع کالاها مانند FEFO یا FIFO و در نظر گرفتن موجودی لحظهای پای کار مواد، قطعات و اندازه بسته (Size Lot) آنها تغذیه کرد. همزمان با ثبت عملکرد تولید، پرسنل مصرف واقعی مواد را اظهار میکنند و این میزان از موجودی پای کار کسر میشود. در نتیجه، همواره میتوان از میزان موجودی مواد و قطعات در خطوط تولید آگاه بود.
-
تولید سفارشی
بسیاری از کسبوکارها به دلیل تنوع محصولات و حق انتخاب مشتری در طراحی محصول، فرایند تولید خود را پس از دریافت سفارش از مشتری شروع میکنند. یکپارچگی و ردیابی عملیات از سفارشگیری تا تولید، برنامهریزی تولید نیمهساختههای مورد نیاز و انبارش و تحویل به موقع محصول به مشتری، از دغدغههای مهم مشتریان است که با فرایند تولید سفارشی راهکاران به خوبی قابل پیشبرد است.
-
یکپارچگی با سایر بخشهای فروش، انبار و لجستیک و بهای تمام شده
نرم افزار تولید راهکاران کمک میکند تا با در نظر گرفتن BOM، موجودی لحظهای پای کار مواد، نیمهساختهها، قطعات مورد نیاز برنامههای تولید و همچنین اندازه بسته آنها، مراکز تولیدی را شارژ کنید. همزمان با ثبت عملکرد تولید، پرسنل مصرف واقعی مواد را اظهار میکنند و این میزان از موجودی پای کار کسر میشود. در نتیجه، همواره از میزان موجودی مواد و قطعات در خطوط تولید آگاه هستید.
-
سفارشگذاری و ثبت عملکرد تولید
برنامههای کلان تولید و سفارش مشتریان به برنامههای عملیاتی کوچکتر در سطح روز و شیفت باید تبدیل شود. در این سطح از برنامهها، از وجود مواد و قطعات مطمئن شده و به هنگام کمبود میتوان اقدامات لازم را انجام داد. با صدور برنامه و ارسال مواد به خطوط تولید، پرسنل تولید آنچه در بازههای زمانی شیفت و روز در خطوط اتفاق میافتد، همانند میزان تولید، مصارف خطوط، انحرافات برنامه، ضایعات و دوبارهکاریها را گزارش میکنند تا علاوه بر تهیه گزارشهای مناسب، در مورد اقدامات بعدی نیز تصمیمگیری شود.
-
مدیریت دوباره کاری و ضایعات
نحوه پیشبرد فرایندهای دوباره کاری و بازیافت ضایعات در اکثر شرکتها به شکل دستی و خارج از سیستمهای اطلاعاتی انجام میشود. در حالی که علاوه بر تاثیر این فرایندها در عملیات پرتکرار و مهم شرکت همچون خروج کالاها از انبار یا محاسبه بهای تمام شده، شفافیت مدیران روی این فرایند و تکرار آنها نیز پایین است. این ماژول علاوه بر امکان پیشبرد این فرایندها در داخل سیستم، شفافیت عملیات و نحوه انجام کارها را برای مدیران بیشتر میکند.
-
مدیریت بچ و ردیابی محصول
راهکار مدیریت بچ راهکاران با امکان ردیابی (Traceability)به شما کمک میکند تا بدانید محصولات چگونه تولید، در کجا نگهداری و درن هایت به چه مشتریانی فروخته شدهاند. در این راهکار برای هر بچ محصول تولید شده، امکان ردیابی تا سطح شیفتهای تولیدی به تفکیک عملیات تولیدی، نتایج آزمایشهای کیفی هر مرحله و تامینکنندگان و بچ مواد اولیه ورودی وجود دارد.
امکانات و ابزارهای ماژول کنترل عملیات تولید
اطلاعات پایه و عمومی
- تعریف مراکز کاری و تجهیزات تولیدی
- تعریف ظرفیت، شیفتهای تولیدی، توقفات ثابت و دورههای کاری هر مرکز
- تعریف ابزار و منابع مورد نیاز تولید
مهندسی محصولات
- تعریف الگوی شناسنامه کالا و تخصیص ویژگیها به ازای هر کالا
- تعریف سیاستهای پیشنهادی مصرف مواد و نیمهساختهها از انبار
- تعریف اقلام مورد نیاز محصول و نیمهساختهها (BOM)
- تعریفBOM مرجع و فانتوم جهت تسهیل در تعریف BOM کالا
- نمایش درختواره ساخت محصولات و نیمه ساخته تا آخرین لایه
- تعریف کالاهای جانبی، جایگزین و درجه پایین
- تعریف فرآیندهای تولید محصولات و نیمهساختهها شامل عملیات اصلی، موازی و جایگزین
- تعریف زمانهای استاندارد، ابزار و منابع مورد نیاز و ویژگیهای مهم عملیات تولیدی
- تعریف عملیات کنترل کیفیت در فرایند تولید و تخصیص ویژگیهای آزمایش به آنها
سفارشگذاری تولید
- ثبت سفارشهای تولید بر مبنای برنامههای MRP و سفارش مشتریان ( Make-To-Stock یا Make-To-Order)
- صدور سفارش تولید برای هر محصول یا نیم ساخته و زمانبندی آن به تفکیک عملیات در هر شیفت
- صدور و تجمیع سفارشات نیمه ساختههای لایه پایین به شکل خودکار
- صدور گروهی سفارشات و انجام عملیات گروهی بر روی آنها
- صدور درخواستهای بازرسی کیفی به شکل خودکار
- اطمینان از کفایت موجودی مواد و قطعات لازم برای پیشبرد برنامههای عملیاتی تولید
- ثبت عملکرد بر مبنای سفارش تولید شامل ضایعات کالای تولیدی، درجات پایین و دوبارهکاریها
ثبت عملکرد تولید
- ثبت عملکرد تولید عملیات به تفکیک مقادیر سالم، دوبارهکاری و ضایعات و زمانهای واقعی
- شناسایی و ثبت کالای جانبی تولید شده در ثبت عملکرد
- شناسایی و ثبت کالای درجه پایین تولید شده در ثبت عملکرد
- ثبت کالاهای ضایعات محصولی و فرایندی و ارسال آنها به انبارهای ضایعاتی
- ثبت مصارف واقعی و مواد مصرفی و مقدار و دلیل ضایعات آنها
- رسید و مصرف خودکار نیمه ساختهها و مواد اولیه در انبارهای میانی و پای کار براساس میزان تولید
- ثبت کارکرد ماشینآلات، پرسنل و دلایل انحراف از برنامه در سند عملکرد تولید
- انتقال کارکرد ابزار و منابع به ماژول نگهداری و تعمیرات جهت انجام سرویسهای PM
- دریافت کالاهای تولید در انبار با مبنای اسناد عملکرد تولید
ارسال مواد و قطعات به مراکز تولید
- آگاهی از موجودی مواد و قطعات پای کار تولید و کنترل مستمر آنها
- صدور درخواست کالا از انبار با در نظر گرفتن BOM و به تفکیک یا تجمیع سفارشهای تولید
- ثبت درخواست کالا به تفکیک سفارش، عملیات و کالای مصرفی
- رزور مواد اولیه مورد نیاز هر سفارش تولیدی
- در نظر گرفتن سیاستهای مصرف کالا (FEFO یا FIFO) هنگام رزرو موجودی
- در نظر گرفتن موجودی اقلام جایگزین در ارسال کالا به مراکز تولیدی
- امکان اضافه کردن و درخواست کالای مازاد نیاز سفارشهای تولید
مدیریت دوبارهکاری و ضایعات
- شناسایی کالاهای ضایعاتی تولیدی در سند عملکرد
- پوشش فرایند دوباره کاریهای حین تولید
- پوشش فرایند دوباره کاریهای کالاهای موجود در انبار (یا برگشتی از مشتری)
- برنامهریزی مجدد و دریافت مواد مورد نیاز برای ثبت عملکردهای دوبارهکاری
تولید سفارشی
- پوشش فرایند تولید سفارشی؛ از سفارشگیری تا تولید و تحویل به موقع محصول به مشتری
- آگاهی از ویژگیهای مورد نیاز مشتریان در سفارشات فروش
- صدور سفارشات تولید مبتنی بر سفارشات فروش
- ردیابی سفارشات فروش در مراحل تولیدی
ردیابی محصول
- ردیابی محصولات از تولید تا نگهداری و فروش
- پوشش ردیابی از نوع بچ، به ازای هر سفارش تولید
- پوشش ردیابی پیشرفته بچ بین مراحل، در سطح سند عملکرد و بین عملیات تولیدی
- ثبت ویژگیها و پارامترهای مهم هر عملیات تولید در بچ
گزارشگیری
- امکان ساخت گزارش های متنوع توسط کاربر در کاوشگر راهکاران
- گزارش جامع مرور تولید
- گزارشهای چاپی و تحلیلی متنوع جهت پیشبرد فرایندها و تصمیمگیری بهتر
برخی از مشتریان راهکار مدیریت تولید همکاران سیستم
تجربه مشتریان از بهکارگیری راهکار مدیریت تولید همکاران سیستم
درخواست جلسه دمو
برای دریافت جلسه دمو و مشاوره رایگان اطلاعات خود را در فرم زیر ثبت کنید، کارشناسان ما در اولین فرصت با شما تماس میگیرند.